Визуализация в бережливом производстве: инструменты и методы
Для кого эта статья:
- специалисты и менеджеры в области производства и управления качеством
- студенты и начинающие профессионалы, интересующиеся бережливым производством и визуализацией
- консультанты и эксперты по оптимизации бизнес-процессов
В мире производства скорость принятия решений и оперативность выявления проблем часто определяют успех предприятия. Визуализация — это мощный инструмент бережливого производства, который превращает скрытые процессы в видимые, неявные проблемы — в очевидные, а сложные данные — в простые для восприятия сигналы. Эта методология позволяет не просто увидеть производство во всей его полноте, но и создать систему, где любая аномалия становится заметной в течение секунд, а не часов или дней. Статья раскроет конкретные инструменты визуализации, которые трансформируют хаос в порядок и неопределенность в прозрачность на пути к эффективному производству. 🔍
Стремитесь стать экспертом в оптимизации бизнес-процессов? Курс «Бизнес-аналитик» с нуля от Skypro — это ваш билет в мир профессиональной визуализации и аналитики. Вы изучите не только теоретические основы бережливого производства, но и получите практические навыки работы с инструментами визуализации, которые сегодня востребованы во всех передовых компаниях. Наши выпускники успешно внедряют методологии канбан и 5S на реальных предприятиях!
Что такое визуализация в бережливом производстве
Визуализация в бережливом производстве — это системный подход к организации рабочего пространства и управлению производственными процессами, основанный на принципе наглядности. Суть этого метода заключается в создании таких условий, при которых все нормы, отклонения, проблемы и статус процессов моментально считываются с помощью визуальных сигналов. 📊
Философия бережливого производства, разработанная компанией Toyota, включает визуализацию как один из ключевых инструментов создания потока ценности без потерь. Согласно статистике, внедрение визуальных элементов управления способно сократить время поиска информации и принятия решений на 50-70%, что непосредственно влияет на рост производительности.
Принципы визуализации в бережливом производстве:
- Наглядность — информация должна быть представлена в понятном визуальном формате
- Своевременность — обновление данных происходит в режиме реального времени
- Доступность — информация видна всем участникам процесса
- Стандартизация — использование унифицированных визуальных элементов
- Активация действий — визуальные сигналы должны стимулировать принятие решений
Компонент визуализации | Назначение | Эффект от применения |
---|---|---|
Цветовая кодировка | Быстрая идентификация статуса, категории, приоритета | Сокращение времени реакции на 35% |
Информационные доски | Централизованное представление ключевых показателей | Повышение осведомленности команды на 60% |
Маркировка зон | Четкое определение мест для материалов и оборудования | Снижение потерь времени на поиск на 45% |
Графики и диаграммы | Анализ тенденций и выявление отклонений | Улучшение прогнозирования на 40% |
Визуализация трансформирует абстрактные концепции и потоки данных в конкретные визуальные образы, что позволяет задействовать мощный механизм визуального восприятия человека. Наш мозг обрабатывает визуальную информацию в 60 000 раз быстрее, чем текст, а запоминает такую информацию на 40% эффективнее.
Целевые области применения визуализации включают:
- Управление рабочим пространством и безопасностью
- Контроль состояния оборудования и инструментов
- Мониторинг материальных потоков и запасов
- Отслеживание качества продукции и выявление дефектов
- Координация действий персонала и коммуникация
В условиях современного производства, когда требования к скорости и точности процессов постоянно растут, визуализация является не просто полезным дополнением, а необходимым фундаментом эффективной организации труда.
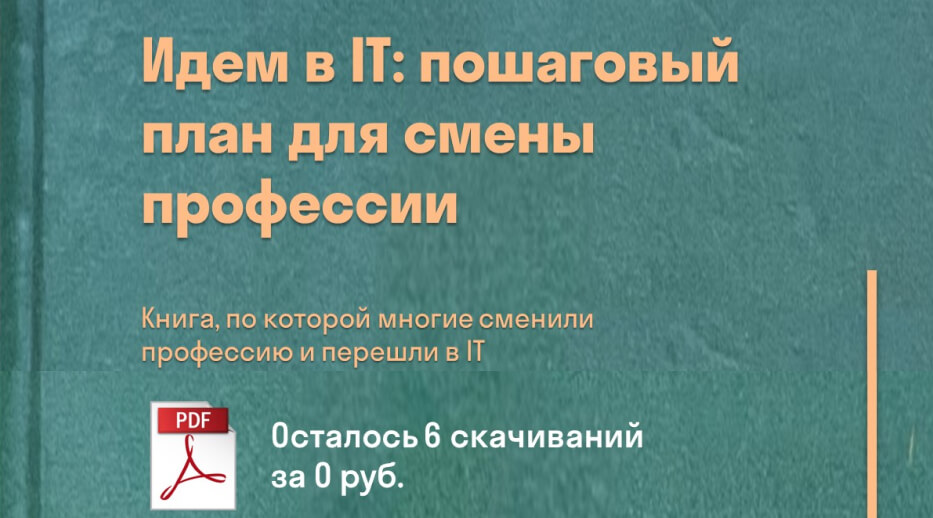
Основные инструменты визуализации для повышения эффективности
Арсенал средств визуализации в бережливом производстве обширен и постоянно пополняется новыми разработками. Эффективное использование этих инструментов позволяет создать систему, где каждый сотрудник от оператора до руководителя моментально получает необходимую информацию о состоянии процессов. 🛠️
Андрей Свиридов, руководитель департамента операционной эффективности: Когда мы начали внедрение инструментов визуализации на нашем предприятии, я был поражен тем, насколько быстро изменилось поведение персонала. Первым шагом стали контрольные листы стандартов операций, размещенные непосредственно на рабочих местах. Через месяц после внедрения количество ошибок сократилось на 23%, а скорость обучения новых сотрудников увеличилась вдвое. Особенно запомнился случай с оператором упаковочной линии, который самостоятельно выявил отклонение в работе оборудования благодаря диаграмме контрольных точек. Это предотвратило выпуск крупной партии бракованной продукции. Визуализация превратила пассивных исполнителей в активных участников системы управления качеством.
Ключевые инструменты визуализации, применяемые на современных производствах:
- Визуальные стандарты работы (SOP) — графические инструкции, иллюстрирующие порядок выполнения операций
- Приборные панели (Dashboard) — цифровые или физические панели с ключевыми показателями эффективности
- Карты потока создания ценности (VSM) — схематическое изображение всех этапов процесса с указанием временных и материальных затрат
- Диаграммы спагетти — визуализация перемещений персонала или материалов для выявления неоптимальных маршрутов
- Оконтуривание инструментов — создание силуэтов для инструментов, обеспечивающее контроль наличия и порядок хранения
Особую ценность представляют контрольные карты и индикаторы состояния процессов, которые позволяют с одного взгляда определять наличие отклонений от нормального течения процесса. Система сигналов светофора (красный-желтый-зеленый) является наиболее распространенной и интуитивно понятной для всех участников производственного процесса.
В 2025 году особенно актуальным становится интеграция цифровых инструментов визуализации с традиционными физическими средствами. Создание "цифровых двойников" производства позволяет отслеживать ключевые параметры в режиме реального времени и прогнозировать возможные проблемы до их возникновения.
Для эффективного внедрения инструментов визуализации необходимо учитывать специфику конкретного производства и адаптировать эти инструменты под его потребности. Универсального решения, подходящего для всех предприятий, не существует.
Инструмент визуализации | Оптимальная область применения | Сложность внедрения (1-10) | Срок получения результатов |
---|---|---|---|
Информационные стенды | Коммуникация KPI команды | 3 | 1-2 недели |
Цветовая маркировка | Складские операции, зонирование | 2 | Мгновенно |
Система андон | Высокоскоростные производственные линии | 8 | 1-3 месяца |
Карты VSM | Анализ потока создания ценности | 7 | 2-4 недели |
Цифровые дэшборды | Интегрированные производственные системы | 9 | 3-6 месяцев |
Важно понимать, что инструменты визуализации не являются самоцелью, а служат средством для создания максимально прозрачной и управляемой производственной системы. Ключевым фактором успеха является не количество внедренных инструментов, а их правильный выбор и корректное применение в соответствии с целями предприятия.
Система 5S как фундамент визуального управления
Система 5S представляет собой методологию организации рабочего пространства, которая не просто служит базой для внедрения инструментов визуализации, но и сама по себе является мощным средством визуального управления. Название происходит от пяти японских слов, начинающихся на "S": Seiri (сортировка), Seiton (соблюдение порядка), Seiso (содержание в чистоте), Seiketsu (стандартизация) и Shitsuke (совершенствование). 🧹
Первый шаг — сортировка (Seiri) — предполагает разделение всех предметов на рабочем месте на необходимые и ненужные с последующим удалением последних. Этот этап часто сопровождается применением "красных ярлыков" — визуальных маркеров, которыми помечаются предметы с неопределенным статусом для дальнейшего принятия решения об их судьбе.
Второй шаг — соблюдение порядка (Seiton) — включает определение оптимального места для каждого предмета и его визуальное обозначение. На этом этапе применяются:
- Контурные маркеры для инструментов и оборудования
- Цветовая кодировка зон хранения различных материалов
- Маркировка пола для обозначения проходов, рабочих зон и зон хранения
- Информационные таблички с указанием наименований и количественных лимитов
Третий шаг — содержание в чистоте (Seiso) — предполагает не только уборку, но и визуальный контроль состояния оборудования. Контрольные листы уборки, графики обслуживания и стандарты чистоты, размещенные на видных местах, являются важными элементами визуализации на этом этапе.
Четвертый шаг — стандартизация (Seiketsu) — закрепляет достигнутые результаты через создание визуальных стандартов. Фотографии эталонного состояния рабочих мест, контрольные листы и инструкции с иллюстрациями помогают поддерживать внедренные улучшения.
Пятый шаг — совершенствование (Shitsuke) — обеспечивает долгосрочное функционирование системы через аудиты, визуальный контроль и обратную связь. Радарные диаграммы оценки соответствия стандартам 5S и информационные стенды с результатами аудитов стимулируют постоянное улучшение.
Марина Кравцова, специалист по внедрению бережливого производства: На металлургическом заводе, где я консультировала проект внедрения 5S, мы столкнулись с сопротивлением персонала инструментального цеха. "Я и так знаю, где что лежит", — типичная фраза, которую мы слышали. Мы решили провести эксперимент: засекли время поиска нескольких инструментов до внедрения системы. Затем применили контурную маркировку, цветовое кодирование и подписи. Через неделю новое измерение показало сокращение времени поиска в 5-8 раз! Настоящий прорыв произошел, когда мастер цеха, ранее скептически настроенный, сам стал инициатором улучшений, заметив, что теперь гораздо быстрее выявляет отсутствующие инструменты. Система 5S превратилась из "японской блажи" в конкретный инструмент, экономящий время и нервы всей команды.
Эффективность системы 5S в качестве фундамента визуального управления обусловлена следующими факторами:
- Создание визуального стандарта "нормального" состояния, позволяющего моментально выявлять отклонения
- Формирование привычки к постоянному наблюдению и реагированию на визуальные сигналы
- Интуитивная понятность системы для всех участников процесса вне зависимости от их опыта
- Возможность постепенного внедрения с получением быстрых результатов на ранних этапах
По данным исследований 2025 года, предприятия, внедрившие систему 5S как основу для дальнейшего развертывания инструментов бережливого производства, демонстрируют на 27% более высокие показатели успешности этих проектов по сравнению с организациями, пропустившими этот этап.
Для эффективного внедрения 5S как фундамента визуального управления рекомендуется:
- Начинать с пилотного участка, где можно быстро продемонстрировать результаты
- Активно вовлекать сотрудников в создание визуальных стандартов
- Документировать состояние "до/после" с помощью фотографий
- Регулярно проводить аудиты с визуализацией результатов
- Связывать систему 5S с ключевыми показателями эффективности предприятия
Канбан и андон: визуальное управление производством
Канбан и андон представляют собой два фундаментальных инструмента визуального управления производственными процессами, разработанные в рамках производственной системы Toyota и впоследствии ставшие универсальными методами управления потоками и состояниями на предприятиях различных отраслей. 🔄
Канбан (в переводе с японского "вывеска" или "сигнал") — это система управления потоками материалов и информации, основанная на принципе "тянущего производства". Суть системы заключается в создании визуальных сигналов для запуска процессов только тогда, когда возникает реальная потребность в их результатах.
Классическая реализация канбан основана на карточках (физических или электронных), которые несут информацию о:
- Наименовании и характеристиках продукта или компонента
- Количестве единиц в партии
- Источнике получения (откуда поступил запрос)
- Месте назначения (куда должен быть доставлен материал)
- Приоритете и сроках выполнения
Современные варианты канбан-систем также включают:
- Электронные табло с цветовой индикацией состояния заказов
- Канбан-доски с карточками или магнитами, отображающими стадии процессов
- Двухконтейнерные системы, где опустошение одного контейнера служит сигналом для пополнения
- QR-коды и RFID-метки для автоматизированного учета движения материалов
Андон (в переводе с японского "лампа" или "сигнал") — система визуальной и звуковой сигнализации о состоянии процессов и возникающих проблемах. В классическом варианте — это сигнальные лампы или табло, сообщающие о нормальном течении процесса или его нарушении.
Основные компоненты системы андон:
- Сигнальные лампы или световые панели для индикации состояния оборудования
- Звуковая сигнализация различных тонов для привлечения внимания
- Информационные табло, отображающие источник проблемы и характер неисправности
- Кнопки или шнуры для активации сигнала сотрудниками при обнаружении проблемы
Интеграция канбан и андон в единую систему визуального управления позволяет создать производственную среду, в которой:
- Состояние процессов становится видимым для всех участников
- Проблемы выявляются и устраняются в режиме реального времени
- Материальные потоки синхронизируются с реальной потребностью
- Ответственность за качество распределяется между всеми участниками процесса
В 2025 году эффективность внедрения канбан и андон определяется не только их правильной технической реализацией, но и степенью вовлеченности персонала. Системы должны быть интуитивно понятны и удобны в использовании для всех сотрудников вне зависимости от их уровня технической подготовки.
Ключевые принципы эффективного внедрения канбан и андон:
- Определение оптимального размера партий и частоты пополнения запасов на основе анализа времени такта
- Прозрачность информации для всех участников процесса
- Стандартизация визуальных сигналов и реакции на них
- Постепенное снижение размера буферных запасов по мере стабилизации процессов
- Регулярный анализ и корректировка параметров системы
Хотите стать востребованным специалистом по оптимизации производственных процессов? Тест на профориентацию от Skypro поможет определить, насколько ваши навыки и характер подходят для карьеры в области бережливого производства. Пройдите бесплатную оценку, чтобы узнать, готовы ли вы к внедрению визуальных инструментов управления, таких как канбан и андон, или каких знаний вам не хватает для успеха в этой динамичной области!
Практическое применение канбан и андон варьируется в зависимости от специфики отрасли. Например, в дискретном производстве канбан часто используется для управления комплектующими между участками, в то время как в непрерывном производстве акцент делается на андон-системы мониторинга состояния оборудования.
Параметр | Канбан | Андон |
---|---|---|
Основная функция | Управление материальными потоками | Сигнализация о состоянии и проблемах |
Тип визуализации | Карточки, контейнеры, электронные табло | Световые сигналы, информационные панели |
Временной горизонт | Планирование на ближайшую перспективу | Мгновенная реакция в реальном времени |
Цель применения | Оптимизация запасов и синхронизация | Быстрое выявление и устранение проблем |
Сложность внедрения | Средняя (требует расчетов и анализа) | От низкой до высокой (зависит от степени автоматизации) |
Эффективность внедрения этих инструментов оценивается через следующие показатели:
- Сокращение времени производственного цикла
- Снижение уровня запасов и незавершенного производства
- Уменьшение времени реакции на возникающие проблемы
- Повышение стабильности качества продукции
- Рост производительности и общей эффективности оборудования (OEE)
Внедрение визуальных инструментов и измерение результатов
Успешное внедрение инструментов визуализации в производственные процессы требует системного подхода и последовательной реализации. Структурированная методология позволяет не только эффективно имплементировать визуальные инструменты, но и корректно оценивать их влияние на ключевые показатели деятельности предприятия. 📈
Процесс внедрения визуальных инструментов можно разделить на следующие этапы:
- Диагностика и определение целей — анализ текущего состояния процессов и выявление областей, где визуализация принесет максимальную пользу
- Выбор инструментов — определение оптимального набора визуальных методов для конкретных производственных условий
- Подготовка персонала — обучение сотрудников принципам работы с визуальными инструментами и формирование соответствующей культуры
- Пилотное внедрение — апробация выбранных инструментов на ограниченном участке производства
- Масштабирование — расширение применения визуальных инструментов на все релевантные процессы
- Стандартизация — закрепление успешных практик в виде корпоративных стандартов
- Непрерывное совершенствование — регулярный аудит и обновление визуальных инструментов
Для каждого этапа внедрения критически важно определить четкие метрики успеха и механизмы их измерения. Наиболее эффективный подход — использование сбалансированной системы показателей, учитывающей как количественные, так и качественные аспекты.
Ключевые показатели эффективности визуальных инструментов:
- Операционные показатели: время цикла, уровень запасов, время переналадки, OEE (Overall Equipment Effectiveness)
- Показатели качества: уровень дефектов, количество переделок, стоимость качества
- Показатели безопасности: частота инцидентов, время реакции на потенциально опасные ситуации
- Финансовые показатели: производственные затраты, ROI от внедрения визуальных инструментов
- Показатели вовлеченности персонала: количество предложений по улучшению, уровень участия в программах непрерывного совершенствования
Для объективной оценки эффективности визуальных инструментов необходимо собирать данные "до" и "после" их внедрения. Современные системы сбора и анализа данных позволяют автоматизировать этот процесс и получать информацию в режиме реального времени.
При организации системы измерения результативности визуализации необходимо учитывать следующие аспекты:
- Определение базовых показателей (baseline) для последующего сравнения
- Выбор адекватной частоты измерений для различных типов показателей
- Создание механизмов валидации полученных данных
- Разработка процедур корректирующих действий при выявлении отклонений
- Формирование системы визуального представления результатов измерений
Согласно данным ведущих консалтинговых компаний, в 2025 году успешные проекты внедрения визуальных инструментов демонстрируют следующие средние показатели улучшений:
Область улучшений | Диапазон эффекта | Средний срок достижения | Устойчивость результата |
---|---|---|---|
Производительность труда | 15-30% | 3-6 месяцев | Высокая |
Снижение уровня запасов | 20-40% | 6-12 месяцев | Средняя |
Сокращение дефектов | 30-60% | 2-4 месяца | Высокая |
Время переналадки оборудования | 40-70% | 1-3 месяца | Высокая |
Своевременность поставок | 15-25% | 3-6 месяцев | Средняя |
Использование производственных площадей | 10-30% | 6-12 месяцев | Высокая |
Одной из ключевых проблем при внедрении визуальных инструментов является поддержание их актуальности в долгосрочной перспективе. Для решения этой задачи рекомендуется:
- Интегрировать аудиты визуальных систем в общую систему управления качеством
- Назначать ответственных за поддержание и обновление визуальных элементов
- Регулярно пересматривать и обновлять содержание информационных панелей
- Проводить конкурсы и мероприятия, стимулирующие использование визуальных инструментов
Важным фактором успеха является также корпоративная культура, поддерживающая принципы визуализации. Необходимо формировать среду, в которой визуальная прозрачность рассматривается не как инструмент контроля, а как средство коллективного решения проблем и повышения эффективности.
Визуализация в бережливом производстве — это не просто набор инструментов, а философия управления, основанная на принципе прозрачности и доступности информации. Эффективное применение описанных методов позволяет трансформировать производственную среду, делая проблемы видимыми, решения очевидными, а процессы управляемыми. Предприятия, внедряющие систему визуального менеджмента, получают не только измеримые экономические преимущества в виде снижения затрат и повышения качества, но и создают культуру непрерывного совершенствования, где каждый сотрудник становится активным участником процесса улучшений. В мире растущей сложности производственных систем именно визуализация становится ключом к сохранению контроля и обеспечению стабильности.