Диаграмма Исикавы: примеры внедрения на производстве – анализ
Пройдите тест, узнайте какой профессии подходите
Для кого эта статья:
- Производственные аналитики и специалисты по контролю качества на заводах
- Руководители и менеджеры производственных процессов
- Студенты и новички, желающие освоить методы анализа данных в производстве
Диаграмма Исикавы – инструмент, превращающий хаос производственных проблем в структурированный анализ. На российских предприятиях, где брак может достигать 15-20%, правильное применение причинно-следственных диаграмм снижает этот показатель до 3-5% уже в течение первых месяцев внедрения. Метод, разработанный японским инженером Каору Исикава в 1960-х, сегодня является критическим элементом системы контроля качества на промышленных объектах мирового уровня. 🔍 Почему же рыбья кость (как её часто называют) остаётся незаменимой в арсенале производственных аналитиков 2025 года?
Хотите овладеть мощными аналитическими инструментами, которые используются на передовых производствах? Курс «Аналитик данных» с нуля от Skypro даст вам не только понимание диаграммы Исикавы, но и комплексный набор методов глубокого анализа производственных процессов. Наши выпускники применяют полученные навыки для снижения брака на 70% и оптимизации производства. Практические кейсы от реальных предприятий сделают вас ценным специалистом на рынке труда.
Суть и значение диаграммы Исикавы в производственном анализе
Диаграмма Исикавы (причинно-следственная диаграмма) — аналитический инструмент, визуализирующий связь между результатом и влияющими на него факторами. Её второе название — "рыбья кость" — объясняет визуальную структуру диаграммы: центральная линия (хребет) ведет к проблеме (голове рыбы), а от неё отходят основные категории причин (кости).
В производственном анализе диаграмма Исикавы выполняет несколько ключевых функций:
- Структурирование причин возникновения дефектов
- Определение взаимосвязей между различными факторами производства
- Фокусировка коллективного мышления на конкретной проблеме
- Визуализация сложных производственных взаимодействий
- Выявление коренных, а не поверхностных причин проблем
Классический подход предполагает разделение причин на шесть основных категорий, формирующих аббревиатуру 5M+E:
Категория | Что включает | Вес в производственном анализе |
---|---|---|
Man (Персонал) | Квалификация, дисциплина, мотивация | 25-30% |
Machine (Оборудование) | Состояние, настройки, техобслуживание | 20-25% |
Material (Материалы) | Качество сырья, комплектующих | 15-20% |
Method (Технология) | Методы работы, инструкции, стандарты | 15-20% |
Measurement (Измерения) | Точность приборов, методика измерений | 5-10% |
Environment (Среда) | Внешние условия, температура, влажность | 5-10% |
Значимость диаграммы Исикавы для производства определяется её способностью превращать абстрактные проблемы в конкретные причины, поддающиеся измерению и устранению. По данным международных исследований, предприятия, систематически применяющие этот метод, сокращают уровень брака на 30-40% и снижают производственные издержки на 15-25% в течение года после внедрения. 📊
В отличие от многих других методов, диаграмма Исикавы не требует сложных математических вычислений или специального программного обеспечения, что делает её доступной для любого производственного предприятия. Тем не менее, эффективность метода зависит от правильного применения и использования объективной информации о процессах.
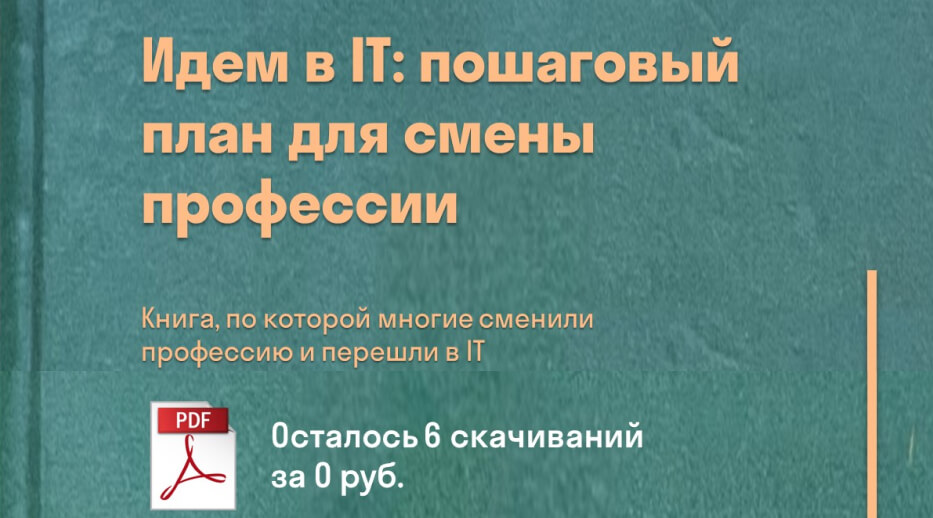
Пошаговое внедрение диаграммы Исикавы на производстве
Внедрение диаграммы Исикавы на производстве — процесс, требующий системного подхода и вовлечения сотрудников разных уровней. Правильная последовательность действий гарантирует не только построение самой диаграммы, но и получение практических результатов от её использования. 🔧
Михаил Соколов, руководитель проектов по оптимизации производства
Когда мы начали внедрять диаграмму Исикавы на производстве автокомпонентов, мы столкнулись с сопротивлением персонала. "Зачем нам еще одна бумажка?" — спрашивали мастера. Я организовал пилотный проект по анализу проблемы с повышенным браком крепежных элементов. Собрал рабочую группу из операторов, технологов и контролеров ОТК, выделил два часа на совместную работу.
Диаграмму рисовали на большом листе на стене цеха, каждый мог подойти и добавить свои идеи. Ключевым моментом стало то, что мы не искали виноватых, а анализировали факторы. Уже через неделю после внедрения первых корректирующих мероприятий брак снизился с 8% до 2,5%. Операторы сами стали просить провести аналогичный анализ для других проблемных участков. Инструмент заработал, когда люди увидели реальный результат.
Алгоритм внедрения диаграммы Исикавы на производстве включает следующую последовательность шагов.
- Определение проблемы: Четко сформулируйте проблему, которую необходимо решить. Например: "Повышенное количество брака при штамповке детали А-1500".
- Формирование команды: Привлеките специалистов разных направлений: технологов, операторов оборудования, инженеров по качеству, ремонтный персонал.
- Подготовка рабочего пространства: Организуйте помещение с большой доской или флип-чартом, позволяющим визуализировать диаграмму.
- Определение основных категорий причин: Стандартные 5M+E или адаптированные под специфику вашего производства.
- Проведение мозгового штурма: Соберите все возможные причины проблемы по каждой категории.
- Структурирование и уточнение причин: Группируйте причины по категориям, выявляйте взаимосвязи.
- Оценка значимости причин: Применяйте методы ранжирования для определения наиболее важных факторов.
- Разработка корректирующих мероприятий: Для каждой ключевой причины определите действия по её устранению.
- Внедрение и мониторинг результатов: Реализуйте корректирующие действия и отслеживайте изменения.
- Стандартизация процедуры: Интегрируйте метод в систему управления качеством предприятия.
Эффективность внедрения зависит от нескольких ключевых факторов:
Фактор успеха | Практические рекомендации |
---|---|
Вовлеченность руководства | Руководители должны лично участвовать в анализе стратегически важных проблем, демонстрируя значимость метода |
Обучение персонала | Проведите тренинги для всех сотрудников, включая операторов линий, по методике построения диаграммы |
Регулярность применения | Внедрите календарь анализа ключевых показателей с использованием диаграммы (еженедельно/ежемесячно) |
Использование цифровых инструментов | Применяйте специализированное ПО для создания, хранения и анализа диаграмм |
Интеграция с другими методами | Комбинируйте диаграмму Исикавы с Парето-анализом и методологией PDCA |
Критически важно соблюдать принцип "фактов и данных", избегая предположений и субъективных мнений при определении причин. Каждая гипотеза должна проверяться с помощью измерений или наблюдений. Современные производства используют данные из MES-систем и промышленного IoT для получения объективной информации о процессах.
Реальные кейсы применения диаграммы Исикавы на заводах
Реальные примеры применения диаграммы Исикавы демонстрируют универсальность и эффективность инструмента в различных производственных ситуациях. Рассмотрим несколько кейсов с конкретными результатами внедрения. ⚙️
Елена Волкова, начальник отдела качества
На нашем фармацевтическом производстве мы столкнулись с проблемой нестабильного веса таблеток в партии. Допуски были критически важны из-за точной дозировки активного вещества. Традиционный подход "настроить оборудование" и "усилить контроль" не давал устойчивого результата.
Мы собрали кросс-функциональную команду и построили диаграмму Исикавы. В категории "Материалы" выявили проблему с нестабильной насыпной плотностью сырья из-за различных поставщиков. В категории "Методы" обнаружили некорректную последовательность загрузки компонентов в смеситель. По категории "Измерения" выяснилось, что калибровка весов проводилась раз в полгода, а дрейф показаний начинался уже через 3-4 месяца.
Корректирующие действия включали введение входного контроля насыпной плотности сырья, стандартизацию методики смешивания и увеличение частоты калибровки весов. За два месяца отклонения веса таблеток сократились с ±4,8% до ±1,2%, что полностью соответствовало требованиям фармакопеи. Диаграмма Исикавы стала для нас не просто инструментом, а способом мышления.
Кейс №1: Металлургический комбинат — решение проблемы трещин при горячей прокатке
Проблема: На прокатном стане появлялись продольные трещины на 18-25% продукции, что приводило к значительным потерям.
Применение диаграммы Исикавы:
- Выявлены 27 потенциальных причин в шести категориях
- Ключевые причины по категориям:
- Оборудование: несоосность валков из-за износа подшипников
- Материал: повышенное содержание серы в определенных партиях заготовок
- Персонал: отсутствие стандартизированных действий при переналадке
- Корректирующие действия:
- Разработка графика упреждающей замены подшипников
- Внедрение дополнительного входного контроля заготовок
- Стандартизация процедуры переналадки
Результат: Через 3 месяца после внедрения уровень дефектов снизился до 3,8%, экономический эффект составил более 50 млн рублей в год.
Кейс №2: Пищевое производство — устранение посторонних включений в продукции
Проблема: Участившиеся случаи обнаружения посторонних включений (пластик, резина) в готовой продукции.
Применение диаграммы Исикавы:
- Рассмотрено 15 потенциальных источников включений
- Основные категории причин:
- Оборудование: износ пластиковых скребков на смесителях
- Методы: отсутствие регламента по проверке целостности оснастки
- Среда: открытые зоны производства без должной защиты
- Внедренные решения:
- Замена пластиковых элементов на металлические детекторы
- Внедрение чек-листов проверки целостности оборудования
- Установка защитных экранов над открытыми зонами
Результат: Количество рекламаций по посторонним включениям сократилось на 92% за первый квартал после внедрения изменений.
Кейс №3: Автомобильный завод — проблема с шумом в трансмиссии
Проблема: Повышенный уровень шума в коробке передач, обнаруживаемый на финальных испытаниях.
Применение диаграммы Исикавы:
- Анализ выявил 32 потенциальные причины
- Основные факторы:
- Материал: отклонения в термообработке шестерен
- Измерения: недостаточная чувствительность акустического контроля на промежуточных этапах
- Персонал: нарушение порядка сборки подшипниковых узлов
- Решения:
- Модернизация процесса термообработки с улучшенным контролем температурных режимов
- Внедрение дополнительных контрольных точек акустического контроля
- Разработка и внедрение поточной СОП по сборке с фото каждой операции
Результат: Уровень шумных трансмиссий снизился с 12,7% до 1,3%, время цикла сборки сократилось на 8%.
Анализ этих кейсов показывает, что эффективность диаграммы Исикавы максимальна при соблюдении нескольких условий:
- Точность формулировки проблемы (конкретный дефект/отклонение, а не обобщенная ситуация)
- Вовлечение в анализ представителей всех связанных с проблемой подразделений
- Фокус на фактических данных и измерениях вместо предположений
- Последовательная реализация корректирующих действий с мониторингом результатов
- Документирование найденных взаимосвязей для предотвращения повторения проблем
Типичные ошибки при построении причинно-следственных связей
Несмотря на свою кажущуюся простоту, диаграмма Исикавы часто становится источником ошибок, снижающих эффективность анализа. Производственные компании сталкиваются с типичными заблуждениями и неточностями при построении причинно-следственных связей. 🚫
Рассмотрим основные ошибки и методы их предотвращения:
Неверная формулировка проблемы
- Ошибка: Слишком общая формулировка ("низкое качество продукции")
- Последствие: Размытый фокус анализа, невозможность выявить конкретные причины
- Решение: Использовать измеримые параметры ("превышение допуска по диаметру отверстия на 0,05-0,08 мм")
Смешивание причин и следствий
- Ошибка: Указание в качестве причин других следствий той же проблемы
- Последствие: Запутанная структура, маскирующая корневые причины
- Решение: Проверка каждой причины методом "5 почему"
Поверхностный анализ без детализации
- Ошибка: Ограничение первым уровнем причин без дальнейшего анализа
- Последствие: Невыявление корневых факторов проблемы
- Решение: Разветвление каждой основной причины минимум на 2-3 уровня глубины
Преобладание субъективных мнений
- Ошибка: Построение диаграммы на основе мнений без фактической проверки
- Последствие: Ложные корреляции, неэффективные корректирующие действия
- Решение: Подтверждение каждой гипотезы данными или экспериментами
Ограничение анализа "удобными" категориями
- Ошибка: Фокус только на технических аспектах при игнорировании организационных факторов
- Последствие: Неполное понимание проблемы, временные решения
- Решение: Обязательное рассмотрение всех категорий 5M+E или адаптированной модели
Особую опасность представляет ловушка "назначения виновных", когда диаграмма Исикавы используется для поиска ответственных лиц, а не системных причин проблем. Это не только снижает эффективность анализа, но и формирует негативное отношение персонала к инструменту.
Распространенные ошибки | Частота возникновения* | Способы предотвращения |
---|---|---|
Игнорирование взаимодействия между причинами разных категорий | 78% | Построение матрицы взаимодействия причин разных категорий |
Выявление симптомов вместо корневых причин | 65% | Внедрение практики последовательного применения метода "5 почему" |
Отсутствие приоритизации выявленных причин | 61% | Применение количественных оценок вероятности и влияния каждой причины |
Неучёт цепных реакций между причинами | 57% | Использование дополнительных связей на диаграмме для отображения взаимовлияний |
Формальный подход к анализу | 52% | Оценка качества диаграммы по количеству выявленных и подтвержденных причин |
*По данным исследования применения инструментов качества на 120 производственных предприятиях России и СНГ (2023-2024)
Для повышения точности анализа причинно-следственных связей рекомендуется:
- Внедрить двухэтапный процесс построения диаграммы: сначала создание максимально полной структуры, затем верификация каждой причины
- Использовать цветовое кодирование для обозначения подтвержденных, предполагаемых и опровергнутых причин
- Ввести количественные оценки влияния каждой причины на проблему
- Регулярно пересматривать диаграмму по мере внедрения корректирующих действий
- Документировать "опровергнутые" причины для расширения базы знаний о процессах
Практика показывает, что компании, избегающие указанных ошибок, получают от применения диаграммы Исикавы на 40-60% более эффективные решения производственных проблем.
Хотите избежать типичных ошибок при внедрении аналитических методов на производстве? Тест на профориентацию от Skypro поможет определить ваши сильные стороны в аналитической работе. Узнайте, какие аспекты производственного анализа, включая построение диаграмм Исикавы, соответствуют вашему мышлению. Результаты теста помогут выбрать оптимальную специализацию и развить навыки работы с причинно-следственными связями в производственных процессах.
Оценка эффективности после внедрения диаграммы Исикавы
Внедрение диаграммы Исикавы как инструмента анализа производственных проблем требует оценки реального эффекта от его использования. Комплексный подход к измерению результативности позволяет не только подтвердить ценность метода, но и постоянно его совершенствовать. 📈
Оценка эффективности внедрения диаграммы Исикавы проводится по следующим ключевым направлениям:
Количественные показатели снижения дефектов
- Снижение процента брака по конкретным видам дефектов
- Сокращение вариативности процесса (уменьшение стандартного отклонения)
- Увеличение показателей возможностей процесса (Cp, Cpk)
- Снижение рекламаций от потребителей
Экономические показатели
- Снижение затрат на устранение дефектов и переработку
- Сокращение потерь от некачественной продукции
- Снижение затрат на входной и промежуточный контроль
- ROI проектов по улучшению качества с использованием диаграммы
Временные показатели
- Сокращение времени на выявление корневых причин проблем
- Уменьшение времени реагирования на возникающие отклонения
- Сокращение длительности производственного цикла
Организационные показатели
- Количество сотрудников, обученных методу
- Частота применения диаграммы в разных подразделениях
- Уровень вовлеченности персонала в решение проблем
- Развитие культуры постоянного совершенствования
Для объективной оценки эффективности внедрения диаграммы Исикавы рекомендуется использовать многоуровневую систему показателей:
Уровень показателя | Примеры метрик | Периодичность измерения |
---|---|---|
Оперативный | Сокращение количества конкретных дефектов, время выявления причин отклонений | Ежедневно/еженедельно |
Тактический | Показатели стабильности процесса, уровень соответствия спецификациям | Ежемесячно |
Стратегический | Доля брака, затраты на качество, удовлетворенность потребителей | Ежеквартально/ежегодно |
Финансовый | ROI от проектов улучшения, снижение себестоимости | Ежеквартально/ежегодно |
Культурно-организационный | Компетентность персонала, инициативность в применении метода | Полугодично/ежегодно |
Статистика по результатам внедрения диаграммы Исикавы на российских производственных предприятиях в 2023-2024 годах показывает следующий средний эффект:
- Снижение уровня брака: 35-48% в течение первого года применения
- Экономический эффект: 5-12 рублей на каждый рубль, вложенный во внедрение метода
- Сокращение времени на решение производственных проблем: 40-60%
- Повышение вовлеченности производственного персонала: 25-30%
Для максимизации эффекта от внедрения диаграммы Исикавы рекомендуется:
- Интегрировать диаграмму с другими инструментами качества (Парето, FMEA, SPC)
- Создать базу знаний по выявленным причинно-следственным связям процессов
- Включить построение диаграмм Исикавы в стандартные процедуры разработки новых продуктов и технологий
- Проводить регулярный аудит эффективности применения метода и корректировать подход к его использованию
- Разработать систему мотивации персонала, стимулирующую активное применение инструмента
Особое внимание следует уделять не только прямому эффекту от решения конкретных проблем, но и долгосрочному влиянию системного применения диаграммы Исикавы на культуру производства и мышление сотрудников. Опыт ведущих компаний показывает, что наибольшую ценность метод приносит, когда становится частью повседневной операционной деятельности, а не эпизодическим инструментом для решения кризисных ситуаций.
Диаграмма Исикавы — больше чем аналитический инструмент. Это фундаментальный сдвиг в производственном мышлении, переход от управления последствиями к управлению причинами. Структурируя кажущийся хаос взаимосвязей, она превращает интуитивные догадки в проверяемые гипотезы, создавая мощный рычаг для системных улучшений. Компании, интегрировавшие этот метод в свою культуру, уже не рассматривают производственные проблемы как случайности — они видят в них возможности для совершенствования процессов и повышения конкурентоспособности.