Основные инструменты бережливого производства: путь к эффективности
Для кого эта статья:
- Руководители и менеджеры производственных предприятий
- Специалисты по оптимизации процессов и Lean-эксперты
- Студенты и профессионалы, заинтересованные в управлении и производственных практиках
Производственную эффективность невозможно завоевать наскоком. Это методичный, выверенный путь трансформации каждого процесса, где каждая секунда, каждый сантиметр пространства и каждый элемент работы находит своё оптимальное место. Бережливое производство — это не просто набор техник, а философия ведения бизнеса, превращающая избыточные затраты и потери в конкурентное преимущество. Согласно исследованиям McKinsey, компании, внедрившие принципы Lean, демонстрируют рост производительности на 15-30% и сокращение затрат до 40%. Давайте рассмотрим инструментарий, который делает эти впечатляющие результаты возможными. 🏭
Столкнулись с проблемой оптимизации производственных процессов? Курс «Менеджер проектов» от Skypro перевернёт ваше представление об управлении ресурсами. Более 87% выпускников курса успешно применили Lean-инструменты в своих компаниях, повысив эффективность в среднем на 22%. На курсе вы не просто изучите теорию — вы создадите собственный план бережливого производства под руководством практикующих Lean-экспертов с опытом внедрения в крупных корпорациях.
Сущность концепции бережливого производства
Бережливое производство (Lean Manufacturing) — система управления, направленная на непрерывное совершенствование процессов через устранение всех видов потерь. Философия Lean зародилась в производственной системе Toyota (TPS) в середине 20-го века и с тех пор трансформировала подход к организации производства во всём мире.
Ключевая идея концепции проста — максимизировать ценность для потребителя при минимизации потерь. Тайити Оно, один из основателей TPS, выделил 7 видов потерь (муда), которые необходимо устранять:
- Перепроизводство — изготовление продукции сверх необходимого количества
- Ожидание — простои оборудования или персонала
- Лишняя транспортировка — избыточное перемещение материалов
- Излишняя обработка — ненужные операции, не создающие ценности
- Запасы — избыточное хранение сырья, материалов, полуфабрикатов
- Движения — нерациональные перемещения работников при выполнении операций
- Дефекты — брак, требующий доработки или утилизации
Позже этот список был дополнен восьмым видом потерь — нереализованным творческим потенциалом сотрудников. 💡
Успех Lean-методологии основан на пяти фундаментальных принципах:
Принцип | Сущность | Результат внедрения |
---|---|---|
Определение ценности | Точное понимание, за что готов платить клиент | Фокусировка ресурсов на создании реальной ценности |
Картирование потока создания ценности | Визуализация всех этапов создания продукта | Выявление и устранение операций, не добавляющих ценности |
Создание потока | Организация непрерывного движения продукта | Минимизация простоев и ускорение производственного цикла |
Вытягивание | Производство только того, что нужно клиенту | Снижение запасов и перепроизводства |
Совершенствование | Постоянное улучшение процессов | Непрерывное повышение эффективности и качества |
Андрей Климов, руководитель производства
Когда я пришёл на завод по производству автокомпонентов, первой моей задачей стало сокращение себестоимости продукции на 15%. Конкуренция была жёсткой, и наши азиатские коллеги предлагали цены на 20% ниже. Классический подход «урезать и сократить» мог дать краткосрочный результат, но убил бы предприятие в долгосрочной перспективе.
Мы начали с картирования потока создания ценности для ключевых изделий. Результаты были отрезвляющими — лишь 12% времени производственного цикла добавляли реальную ценность. Остальное — ожидание, перемещения, исправление дефектов.
За шесть месяцев методичного внедрения принципов бережливого производства мы сократили производственный цикл на 43%, уменьшили запасы на складах на 31% и, что удивительно, повысили качество продукции, снизив уровень дефектов с 3,2% до 0,8%. Себестоимость в итоге упала на 22%, что превысило исходную задачу. При этом мы не сократили ни одного сотрудника — люди стали нашим главным ресурсом улучшений, подавая в среднем 2,7 предложения по оптимизации на человека в месяц.
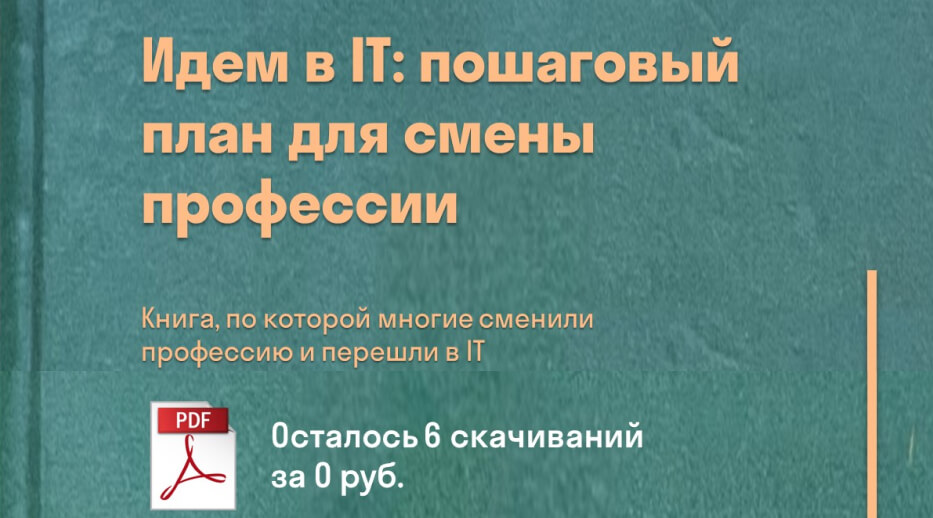
Базовые инструменты системы Lean-менеджмента
Арсенал Lean-менеджмента впечатляет своим разнообразием. Каждый инструмент решает определённую задачу, но максимальная эффективность достигается при их системном применении. Рассмотрим ключевые инструменты, формирующие фундамент бережливого производства:
- Кайдзен (Kaizen) — практика непрерывных малых улучшений, вовлекающая каждого сотрудника
- 5S — система организации рабочего пространства
- Канбан (Kanban) — метод управления производством на основе карточек
- Just-in-Time (JIT) — принцип "точно в срок", минимизирующий запасы
- TPM (Total Productive Maintenance) — всеобщее производительное обслуживание
- SMED (Single-Minute Exchange of Die) — быстрая переналадка оборудования
- VSM (Value Stream Mapping) — картирование потока создания ценности
- Пока-ёкэ (Poka-yoke) — защита от непреднамеренных ошибок
- Гемба (Gemba) — управление на основе наблюдения за реальными процессами
Для эффективного внедрения важно понимать взаимосвязь между этими инструментами и последовательность их применения. Опыт показывает, что начинать обычно следует с 5S и визуального управления, создавая базовый порядок для дальнейших улучшений. 🔄
Инструмент | Основное назначение | Сложность внедрения | Типичный эффект |
---|---|---|---|
5S | Организация рабочего места | Низкая | ↑ Производительность на 10-20%<br>↓ Время поиска на 50-80% |
Канбан | Балансировка производства | Средняя | ↓ Запасы на 25-75%<br>↑ Оборачиваемость на 30-50% |
VSM | Анализ и оптимизация процессов | Высокая | ↓ Время производственного цикла на 30-60% |
SMED | Сокращение времени переналадки | Средняя | ↓ Время переналадки на 50-90%<br>↑ Гибкость производства |
TPM | Повышение надёжности оборудования | Высокая | ↑ OEE на 15-35%<br>↓ Аварийные простои на 50-80% |
Важно отметить, что технический аспект внедрения инструментов Lean составляет лишь 20% успеха. Оставшиеся 80% — это изменение корпоративной культуры, преодоление сопротивления изменениям и создание устойчивой системы непрерывного совершенствования, в которую вовлечен каждый сотрудник от рабочего до генерального директора.
5S: организация рабочего пространства на производстве
Система 5S представляет собой методологию организации, стандартизации и поддержания порядка на рабочем месте. Это фундамент бережливого производства, без которого невозможно эффективное внедрение более сложных инструментов. 5S — это не просто уборка, а системный подход к оптимизации рабочего пространства, повышающий производительность, безопасность и моральный дух коллектива. 📊
Название 5S происходит от пяти японских слов, начинающихся с буквы "С" в английской транслитерации:
- Сортировка (Seiri) — четкое разделение предметов на нужные и ненужные для выполнения работы, избавление от всего лишнего
- Соблюдение порядка (Seiton) — организация хранения необходимых предметов для обеспечения быстрого и простого доступа к ним
- Содержание в чистоте (Seiso) — регулярная уборка рабочего места для поддержания чистоты и порядка
- Стандартизация (Seiketsu) — разработка единых правил и стандартов поддержания порядка
- Совершенствование (Shitsuke) — формирование привычки ежедневного выполнения установленных процедур
Исследования McKinsey (2024) показывают, что правильное внедрение системы 5S приводит к:
- Сокращению времени поиска инструментов и компонентов на 50-80%
- Увеличению полезного пространства на 10-30%
- Сокращению травматизма на 30-50%
- Повышению производительности труда на 10-15%
- Снижению дефектов из-за неправильного хранения на 25-40%
Елена Сорокина, консультант по оптимизации производства
Однажды меня пригласили на небольшое мебельное производство с задачей "навести порядок в цехе". Владелец бизнеса жаловался на постоянные срывы сроков и непонятно высокую себестоимость изделий. Когда я впервые вошла в производственное помещение, картина была типичной — хаос из заготовок, инструментов и материалов.
Мы начали с проведения "красной метки" — акции по выявлению ненужных предметов. За два дня собрали более 200 кг металлолома, обнаружили дублирующие инструменты и залежи материалов с истекшим сроком годности. Сотрудники были в шоке, когда узнали, что компания тратила около 120 000 рублей в месяц на закупку материалов, которые уже имелись на складе, но "затерялись".
На втором этапе разработали схему размещения оборудования и материалов, внедрили цветовую маркировку, ввели теневые панели для инструментов. Сопротивление было жёстким — "мы всегда так работали", "я и так знаю, где что лежит". Переломный момент наступил, когда мастер участка, главный скептик изменений, сам признал, что теперь тратит на 30 минут меньше на подготовку к началу смены.
Через три месяца после внедрения 5S производительность выросла на 23%, количество рекламаций снизилось на 47%, а время выполнения стандартного заказа сократилось с 14 до 9 дней. Но самое удивительное — люди перестали опаздывать на работу. Как выяснилось позже, созданная атмосфера порядка и организованности психологически вызывала желание соответствовать новым стандартам во всём.
Внедрение системы 5S начинается с обучения персонала и пилотного проекта, обычно на одном участке. После достижения видимых результатов практику распространяют на всё предприятие. Ключевые шаги внедрения:
- Проведение аудита текущего состояния рабочих мест (с фотофиксацией)
- Обучение сотрудников принципам 5S
- Выполнение сортировки с применением метода "красных меток"
- Определение мест для всех необходимых предметов
- Тщательная очистка рабочего пространства
- Разработка стандартов поддержания порядка (стандартные операционные процедуры)
- Внедрение системы регулярных аудитов 5S
- Визуализация результатов и поощрение лучших практик
Карта потока создания ценности и канбан-системы
Картирование потока создания ценности (Value Stream Mapping, VSM) и канбан-системы — это мощные инструменты, позволяющие оптимизировать движение материалов и информации в производственной системе. Они помогают визуализировать, анализировать и совершенствовать процессы, устраняя потери и сокращая время производственного цикла. 🔄
VSM — это графическое представление всего процесса создания продукта от поставщика до потребителя. Этот метод позволяет увидеть "большую картину" и идентифицировать операции, добавляющие и не добавляющие ценность. Процесс картирования включает следующие этапы:
- Выбор конкретного продукта или семейства продуктов
- Создание карты текущего состояния (current state map)
- Анализ потерь и возможностей для улучшения
- Разработка карты будущего состояния (future state map)
- Создание плана улучшений и его реализация
При анализе VSM особое внимание уделяют следующим показателям:
- Время цикла (Cycle Time, CT) — время, необходимое для выполнения одной операции
- Время переналадки (Changeover Time, C/O) — время для переключения между производством разных продуктов
- Время такта (Takt Time) — доступное производственное время, делённое на потребительский спрос
- Запасы между операциями (Inventory) — объём материалов/изделий в ожидании обработки
- Доступность оборудования (Uptime) — процент времени, когда оборудование готово к работе
Канбан — это система управления производством и запасами, основанная на принципе "вытягивания". Слово "канбан" по-японски означает "вывеска" или "карточка". В традиционном виде канбан представляет собой карточки, которые сигнализируют о необходимости пополнения запасов или производства определенного количества продукции. 📝
Существует несколько типов канбан-систем:
Тип канбана | Назначение | Применение |
---|---|---|
Производственный канбан | Сигнал о необходимости произвести определённое количество продукции | Внутрипроизводственные процессы, серийное производство |
Транспортный канбан | Указание перемещать материалы между рабочими центрами | Логистика между участками, поставка комплектующих |
Канбан поставщика | Сигнал внешнему поставщику о необходимости поставки | Управление поставками от внешних партнёров |
Электронный канбан | Цифровой аналог физических карточек | Интегрированные производственные системы, ERP |
Двухбункерный канбан | Система с двумя ёмкостями для хранения | Мелкие комплектующие, расходные материалы |
Для правильного расчёта количества канбан-карточек используется формула:
N = D × L × (1 + α) ÷ C
где:
- N — количество канбан-карт
- D — средний дневной спрос на продукт
- L — время пополнения запаса (лид-тайм)
- α — коэффициент безопасности (обычно 0,1-0,3)
- C — ёмкость контейнера
Преимущества интеграции VSM и канбан-систем:
- Снижение уровня запасов на 30-90%
- Сокращение времени производственного цикла на 40-80%
- Повышение оборачиваемости запасов в 2-4 раза
- Улучшение реакции на изменения потребительского спроса
- Визуализация проблем с качеством и узких мест
- Упрощение планирования производства
Современные технологии позволяют создавать цифровые канбан-системы и интерактивные карты потока ценности, которые автоматически корректируются при изменении производственных параметров, что позволяет оперативно реагировать на любые изменения в производственной среде.
Ищете новые горизонты профессионального развития в сфере оптимизации производства? Тест на профориентацию от Skypro поможет определить, насколько вам подходит роль Lean-эксперта или менеджера по оптимизации процессов. Инструменты бережливого производства имеют свою специфику, и не каждому руководителю комфортно работать с методологией непрерывных улучшений. Узнайте за 10 минут, соответствуют ли ваши личностные качества требованиям современных Lean-трансформаций, и получите персональные рекомендации по карьерному росту.
Внедрение инструментов бережливости на предприятии
Успешное внедрение бережливого производства требует системного подхода и преодоления ряда типичных препятствий. Согласно статистике, до 70% первичных инициатив по внедрению Lean терпят неудачу не из-за технических сложностей, а из-за организационных и культурных барьеров. Рассмотрим структурированный подход к трансформации производства на принципах бережливости. 🏭
Дорожная карта внедрения инструментов бережливого производства включает следующие этапы:
- Подготовка и обучение — формирование понимания принципов и инструментов Lean у руководства и ключевых сотрудников
- Диагностика текущего состояния — анализ процессов, определение ключевых показателей эффективности, выявление потерь
- Пилотный проект — выбор ограниченной области для демонстрации эффективности методологии
- Масштабирование — распространение успешных практик на другие участки и процессы
- Стандартизация и закрепление — разработка стандартов, обеспечивающих устойчивость изменений
Критические факторы успеха при внедрении бережливого производства:
- Лидерство и приверженность руководства (top-down подход)
- Вовлечение сотрудников на всех уровнях (bottom-up инициативы)
- Фокус на долгосрочные результаты, а не на быстрые победы
- Систематический подход к измерению результатов
- Прозрачная коммуникация целей и достижений
- Интеграция Lean-инструментов в бизнес-стратегию компании
Типичные ошибки при внедрении и способы их предотвращения:
Распространённая ошибка | Последствия | Рекомендуемое решение |
---|---|---|
Внедрение инструментов без понимания философии | Формальный подход, отсутствие системных улучшений | Начать с обучения принципам и ценностям Lean |
Отсутствие измеримых целей | Невозможность оценить эффективность внедрения | Определить чёткие KPI для каждой инициативы |
Недостаточное вовлечение сотрудников | Сопротивление изменениям, саботаж | Создать систему поощрения предложений по улучшению |
Попытка внедрить все инструменты сразу | Распыление ресурсов, отсутствие видимых результатов | Начать с базовых инструментов (5S, визуальное управление) |
Игнорирование культурных аспектов | Временный эффект без устойчивых изменений | Интегрировать принципы Lean в корпоративную культуру |
Поэтапное внедрение инструментов бережливого производства обычно следует определённой логике:
- Стабилизация процессов (5S, стандартизация работы, визуальное управление)
- Оптимизация потоков (VSM, канбан, балансировка линий)
- Повышение гибкости (SMED, TPM, Poka-yoke)
- Совершенствование системы (кайдзен, дзидока, шесть сигм)
Согласно исследованию Lean Enterprise Institute (2025), компании, которые успешно внедрили принципы бережливого производства, демонстрируют следующие результаты:
- Сокращение производственного цикла на 50-70%
- Повышение производительности на 25-40%
- Снижение уровня дефектов на 60-90%
- Сокращение производственных площадей на 30-50%
- Уменьшение запасов на 50-80%
- Повышение показателя OEE (Overall Equipment Effectiveness) на 20-30%
Важно помнить, что внедрение бережливого производства — это не проект с фиксированной датой завершения, а непрерывный процесс совершенствования. Японская концепция "кайдзен" предполагает, что нет предела совершенству, и каждый день должен завершаться немного лучше, чем начался.
Бережливое производство — не просто набор техник и методов, а философия постоянного совершенствования, увлекательный путь, где каждый шаг приближает предприятие к идеальному состоянию операционной эффективности. Организации, сумевшие внедрить эту культуру непрерывных улучшений, получают не только конкурентные преимущества сегодня, но и устойчивую платформу для развития в будущем. Помните: истинная ценность Lean не в самих инструментах, а в людях, которые их применяют, и в их неустанном стремлении к совершенству. Начните с малого, будьте последовательны и дайте каждому сотруднику возможность стать агентом перемен — и результаты превзойдут ваши ожидания.